Product Series
Equipment Description: Under the action of the twin-screw, the material enters the pulverization chamber at a uniform speed. The feed port is located in the center of the pulverization chamber. Inside the pulverization chamber, there is a high-speed rotating needle disk rotor and a stationary needle disk stator. The annular needle bars of the two needle disks are alternately interlocked. The high-speed rotation of the rotor needle disk generates centrifugal force. The material enters from the center of the stator needle disk and, under the action of centrifugal force, passes through the needle bar forests of the two needle disks at high speed. The material and material and the material and the needle bar produce a large number of impacts, thereby achieving the effect of pulverization. In this process, the linear velocity of the material can reach 200m/s, and the minimum pulverization particle size can reach 9μm (D90).
Equipment Description: Under the impetus of the twin-screw, the material enters the pulverizing chamber at a uniform speed. The feed port is located in the center of the pulverizing chamber. Inside the pulverizing chamber are a high-speed rotating rotor and a stationary stator, both with annular needle bars interlocked alternately. The high-speed rotation of the rotor generates centrifugal force. The material enters from the center of the stator, and under the action of centrifugal force, it passes rapidly through the needle bars of the two discs. The material collides repeatedly with itself and the needle bars, achieving a pulverizing effect. In this process, the linear velocity of the material can reach up to 200 m/s, and the minimum pulverized particle size can reach 9 μm (D90).
Equipment Description: This equipment adopts a modular integrated design, with a minimum particle size of 30μm for hammer crushing. It uses a brushless DC motor drive and a DC speed regulator knob for speed regulation, with a wide speed regulation range (1000~15000r/min), constant low-speed torque, and long motor life. The installation is accurate and reliable; disassembly and cleaning are convenient. Working Principle: The hammer crusher is mainly suitable for hammer crushing processes; the working principle is that the rotor with blades rotates at high speed, forming a high-speed relative motion with the precision small-diameter screen mesh, and the material is crushed by the hammer and blade edges of the rotor. Applications: The hammer crusher is especially suitable for crushing hard, crystalline, and fibrous products, as well as some products that require very fine particles, and is an ideal equipment for processing the particle size of raw materials (API). Technical Features: 1. Flexible modular design, independent electrical control. 2. High speed, high efficiency. 3. Materials will not adhere to the shell, easy to clean. 4. Waterproof, dustproof, and explosion-proof options are available according to requirements. 5. Suitable for fine crushing of hard blocks, crystals, or fibrous materials. 6. Material in-place detection to improve work continuity. 7. Uniform feeding device with dust-free sealing of the hammer crusher. 8. The rotor and screen mesh can be quickly and easily disassembled. 9. Equipped with a twin-screw feeding mechanism to achieve uniform material feeding. 10. Quick-connect, easy to disassemble and clean. 11. Optional vacuum feeding, low labor intensity, and high work efficiency. 12. Wide range of applications (30~150μm), can crush various materials with different properties. 13. Triple sealing of the main shaft and crushing chamber (positive pressure sealing, lip sealing, synchronous material throwing disc) to effectively prevent material contamination. 14. The control cabinet is fully enclosed, and both the air intake and exhaust use forced fans, and both the air intake and exhaust ports are equipped with H13 high-efficiency filters to effectively prevent dust from entering the cabinet. 15. The water-cooled channel interface uses Staubli (Switzerland Staubli) quick connectors, with a life of 107 (one million) insertions and withdrawals, and the socket has an automatically closing shut-off valve, so there will be no gas or liquid leakage after disconnection, which is conducive to stable production. Technical Parameters:
Equipment Overview: When materials rotate at high speed in the grinding chamber, the material particles rub against each other, and the particles become smaller and smaller. When the centrifugal force is less than the force generated by the airflow at the center discharge port, the material will be carried out of the discharge port with the airflow. Working Principle: Feeding: Raw materials are fed uniformly through the feeder, and the materials are sucked into the grinding chamber by the negative pressure generated by the gas injected through the inlet. Grinding: The materials rotate at high speed in the cavity along the set direction, causing the materials to collide and rub against each other, grinding the materials. Collection: Most of the ultrafine materials after crushing enter the material storage container. Dust removal: A very small part of the material is taken to the dust collector, and after filtration, the clean air is discharged. Applications: ★Suitable for dry ultrafine crushing of various brittle, crystalline, heat-sensitive, and medium-low hardness materials. ★Applied to chemical, pharmaceutical, and food industries, with high efficiency and no dust leakage. ★For various particles between 1~50μm in target particle size. Technical Characteristics: ●Low-temperature, medium-free crushing, especially suitable for crushing heat-sensitive, low-melting-point, sugar-containing, and volatile materials. ●Equipped with a precision powder feeding mechanism with weighing feedback control, which can accurately feed powder. ●Equipped with three types of angle airflow nozzles, suitable for crushing materials with different properties. ●The whole system is closed for crushing, with less dust, low noise, and a clean and environmentally friendly production process. ●Each component is detachable, without dead corners, easy to clean and disinfect; simple and quick installation, easy for operators to master. Technical Parameters:
Mobile grain cleaner ZLJ-270-Y
Working principle: This machine utilizes the high-speed relative motion between the rotor and the screen to quickly granulate the block-like materials under the pressure of the rotor, passing through the screen holes. The finished granules are discharged instantly, resulting in less heat generation, high efficiency, and good quality. It adopts frequency conversion speed regulation, the main shaft speed is adjustable, and the range is wide. The lower drive ensures smooth feeding. The parts of the machine that contact the materials and the external parts are made of high-quality stainless steel with a polished surface. It can be used with wet granulation machines and fluidized bed drying equipment.
Mobile whole grain machine ZLJ-140-Y
Working principle: The pellet mill utilizes the high-speed relative motion between the rotor and the screen to quickly break down the clump-like materials under the pressure of the rotor, forming pellets through the screen holes. Finished pellets are instantly discharged, resulting in low heat generation, high efficiency, and good quality. Variable frequency speed regulation allows for adjustable main shaft speed with a wide range. Lower drive ensures smooth feeding. The parts of the machine that come into contact with materials and the exterior are made of high-quality stainless steel with a polished surface. It can be used with wet granulation machines and fluidized bed drying equipment.
Working Principle: The whole grain machine utilizes the high-speed relative motion between the rotor and the screen to quickly break down clump-like materials. Under the rolling pressure of the rotor, these materials pass through the screen holes to form granules. Finished granules are discharged instantly, resulting in less heat generation, high efficiency, and good quality.
Applications: Primarily used for wet granulation and spray granulation of clump-like materials and unqualified tablets. It can process materials to meet various particle size requirements. It can also be used for the recycling of food and biscuit crumbs and for the crushing and granulation of other coarse materials. It is an ideal device for processing low-viscosity, block-like, gum-like, and moist materials.
Technical Features:
● Modular design, enabling dry and wet granulation by changing granulation knives and screens.
● Screen openings as small as φ0.4mm, high opening rate, no dead corners; fine granulation particle size, high material throughput, effectively reducing the occurrence of material heating, easy to clean.
● High screen aperture accuracy, precisely controllable gap between the granulation knife and the screen, precise control of the particle size distribution of the material after granulation.
● Self-designed right-angle transmission system and shaft sealing technology, reducing the risk of material contamination.
● The entire working cavity is smoothly transitioned without dead corners, ensuring smooth material flow, less residue, and high yield.
● The entire machine uses quick-release clamps for simple and fast disassembly and installation, easy for operators to master.
Contact Information
Telephone
/ TEL
Address
/ ADD
No. 2, No. 712 Xiangfu Avenue, Shuangfu Street, jiangjin district, Chongqing
Scan mobile websites
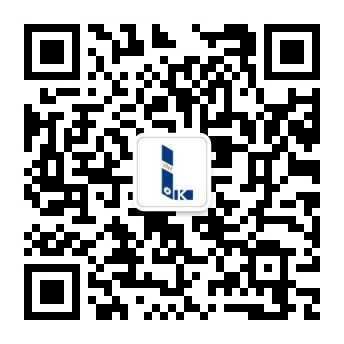