Product Series
Multifunctional whole grain crushing and screening integrated machine S-LAB
The multifunctional experimental machine adopts a modular design. By changing the head, the function can be switched. It can be switched to whole-grain function, screening function, hammer crushing function, and an optional twin-screw powder feeding system.
High-efficiency wet granulator
Working principle: Powdery materials are mixed in a sealed container through the rotation of the stirring paddle to form a semi-fluid state, allowing for complete mixing; meanwhile, a binder and an appropriate amount of water are injected, forming moist soft material, which is then chopped by the high-speed rotation of the horizontal cutting knife and made into uniform moist granules through the granulation mechanism. This equipment is widely used in the pharmaceutical, food, and chemical industries and is an ideal equipment for laboratory process exploration and practical teaching.
My company offers pneumatic butterfly valves in various specifications. Welcome to place your order!
Rotary swaging and extrusion rounding machine
Product Overview: Utilizing twin-blade rotary extrusion, the feed blade and extrusion blade, combined with low-shear technology, reduce energy consumption and temperature rise, enabling adaptability to a wide range of materials and making it ideal for processing sensitive materials. Multiple screen models are available to optimize particle size, surface quality, and particle size distribution. Suitable for batch and continuous production. Modular design facilitates cleaning.
The YB-160 oscillating granulator is a specialized device that uses the forward and reverse rotation of a rotating drum to force a wet powder mixture through a screen to produce granules. It is an innovative and optimized granulator designed by our company to meet the needs of our customers and to seamlessly connect with highly efficient wet granulation processes.
The multifunctional fluidized bed is a multifunctional granulation and drying equipment that uses negative pressure boiling fluidization technology and spray drying technology to achieve heat and mass transfer for material granulation, coating, and pelletizing. The system adopts PLC program control technology and air intake proportion control technology, making the granulation, coating, and pelletizing drying process stable, highly efficient, and highly automated. It is suitable for granulating, coating, and pelletizing powders and granular materials, and is widely used in the material granulation and drying processes in the pharmaceutical, food, chemical, and feed industries.
Equipment Description: Under the action of the twin-screw, the material enters the pulverization chamber at a uniform speed. The feed port is located in the center of the pulverization chamber. Inside the pulverization chamber, there is a high-speed rotating needle disk rotor and a stationary needle disk stator. The annular needle bars of the two needle disks are alternately interlocked. The high-speed rotation of the rotor needle disk generates centrifugal force. The material enters from the center of the stator needle disk and, under the action of centrifugal force, passes through the needle bar forests of the two needle disks at high speed. The material and material and the material and the needle bar produce a large number of impacts, thereby achieving the effect of pulverization. In this process, the linear velocity of the material can reach 200m/s, and the minimum pulverization particle size can reach 9μm (D90).
Equipment Description: Under the impetus of the twin-screw, the material enters the pulverizing chamber at a uniform speed. The feed port is located in the center of the pulverizing chamber. Inside the pulverizing chamber are a high-speed rotating rotor and a stationary stator, both with annular needle bars interlocked alternately. The high-speed rotation of the rotor generates centrifugal force. The material enters from the center of the stator, and under the action of centrifugal force, it passes rapidly through the needle bars of the two discs. The material collides repeatedly with itself and the needle bars, achieving a pulverizing effect. In this process, the linear velocity of the material can reach up to 200 m/s, and the minimum pulverized particle size can reach 9 μm (D90).
Equipment Description: This equipment adopts a modular integrated design, with a minimum particle size of 30μm for hammer crushing. It uses a brushless DC motor drive and a DC speed regulator knob for speed regulation, with a wide speed regulation range (1000~15000r/min), constant low-speed torque, and long motor life. The installation is accurate and reliable; disassembly and cleaning are convenient. Working Principle: The hammer crusher is mainly suitable for hammer crushing processes; the working principle is that the rotor with blades rotates at high speed, forming a high-speed relative motion with the precision small-diameter screen mesh, and the material is crushed by the hammer and blade edges of the rotor. Applications: The hammer crusher is especially suitable for crushing hard, crystalline, and fibrous products, as well as some products that require very fine particles, and is an ideal equipment for processing the particle size of raw materials (API). Technical Features: 1. Flexible modular design, independent electrical control. 2. High speed, high efficiency. 3. Materials will not adhere to the shell, easy to clean. 4. Waterproof, dustproof, and explosion-proof options are available according to requirements. 5. Suitable for fine crushing of hard blocks, crystals, or fibrous materials. 6. Material in-place detection to improve work continuity. 7. Uniform feeding device with dust-free sealing of the hammer crusher. 8. The rotor and screen mesh can be quickly and easily disassembled. 9. Equipped with a twin-screw feeding mechanism to achieve uniform material feeding. 10. Quick-connect, easy to disassemble and clean. 11. Optional vacuum feeding, low labor intensity, and high work efficiency. 12. Wide range of applications (30~150μm), can crush various materials with different properties. 13. Triple sealing of the main shaft and crushing chamber (positive pressure sealing, lip sealing, synchronous material throwing disc) to effectively prevent material contamination. 14. The control cabinet is fully enclosed, and both the air intake and exhaust use forced fans, and both the air intake and exhaust ports are equipped with H13 high-efficiency filters to effectively prevent dust from entering the cabinet. 15. The water-cooled channel interface uses Staubli (Switzerland Staubli) quick connectors, with a life of 107 (one million) insertions and withdrawals, and the socket has an automatically closing shut-off valve, so there will be no gas or liquid leakage after disconnection, which is conducive to stable production. Technical Parameters:
Contact Information
Telephone
/ TEL
Address
/ ADD
No. 2, No. 712 Xiangfu Avenue, Shuangfu Street, jiangjin district, Chongqing
Scan mobile websites
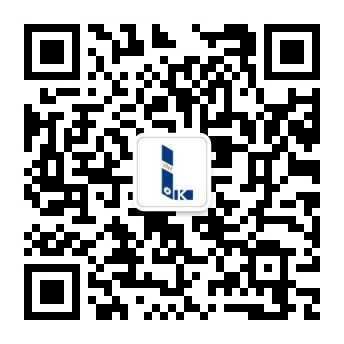