Extrusion Rounding Machine
Product Introduction: The extrusion rolling machine is mainly suitable for microsphere preparation technology. Its working principle is to use a rotating screw to convey and extrude wet raw materials to a spherical dome. The spherical dome extrudes the materials into strips, and then uses a high-speed rotating gear disc to roll the strip-shaped materials into dense spherical microspheres. Microspheres have been widely used in the field of pharmaceutics. As a drug carrier, it can be further pressed into tablets or filled into empty capsules. It not only improves drug stability but also effectively regulates the drug release rate; as a drug delivery system, microspheres have therapeutic advantages, such as less gastrointestinal irritation and reduced risk of drug burst release, improving drug safety and good blood drug concentration reproducibility; microspheres also have good fluidity, low friability, easy filling and other process advantages. In pharmaceutical production, compared with other methods of making pills, extrusion rolling technology is an advanced process method widely used in the international pharmaceutical industry. In controlled-release preparations and drug utilization, many factors in extrusion rolling can change the powder properties of microspheres and the release behavior of drugs; the measurement indicators of microsphere quality mainly include: microsphere particle size, roundness, friability, density, fluidity, drug dissolution and the microstructure of the microsphere surface, etc. Through independent and detailed examination of various factors, the properties of microspheres can be improved purposefully to achieve the expected drug purpose.
Key words: liquid particle handling system solid particle handling system pharmaceutical preparation intelligent equipment equipment intelligent control technology
Classification:
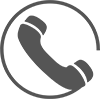
Hotline:
Extrusion Rounding Machine
Product Introduction:
The extrusion spheronizer is mainly suitable for microsphere preparation processes. Its working principle is to use a rotating screw to convey and extrude wet raw materials to a sphere cap. The sphere cap extrudes the materials into strips, and then a high-speed rotating disc rolls the strip-shaped materials into dense spherical microspheres.
Microspheres have been widely used in the field of pharmaceutics. As a drug carrier, it can be further pressed into tablets or filled into empty capsules. It not only improves drug stability but also effectively regulates the drug release rate; as a drug delivery system, microspheres have therapeutic advantages, such as less gastrointestinal irritation and reduced risk of drug burst release, improving drug safety and good blood concentration reproducibility; microspheres also have good fluidity, low friability, and easy filling process advantages.
In pharmaceutical production, compared with other pelletizing methods, extrusion spheronization technology is an advanced process widely used in the international pharmaceutical industry.
In controlled-release preparations and drug utilization, many factors in extrusion spheronization can change the powder properties of microspheres and drug release behavior; the measurement indicators of microsphere quality mainly include: microsphere particle size, roundness, friability, density, fluidity, drug dissolution, and the microstructure of the microsphere surface, etc. Through independent and detailed investigation of various factors, the properties of microspheres can be improved purposefully to achieve the desired medication purpose.
Technical Features:
★ Screw types include double-head equidistant screw, double-head variable-pitch screw, and combination screw, optional. The modular screw selection is suitable for various materials with different properties, making it more versatile.
★ The extrusion barrel has built-in cooling channels to effectively reduce the temperature rise during the extrusion process.
★ Five-axis machined sphere cap, all holes are normal to the surface, resulting in low resistance, low heat generation, smooth material discharge, and long service life.
● Modular design, optional spherical extrusion, lateral extrusion, and plane cutting extrusion.
● The extrusion sphere cap uses five-axis drilling, making material extrusion balanced and efficient.
● Built-in cooling channels for air cooling and water cooling.
● Material and cooling water temperature detection, extrusion current detection, and overload current protection are designed.
● Three types of turntables (optical disc, orthogonal gear disc, and divergent gear disc are optional), suitable for various materials with different properties.
● The process operation is carried out in a wet state, completely eliminating dust.
● High product yield, narrow particle size distribution, and a qualified product rate as high as 90%.
● High efficiency, low cost, and low labor intensity.
Technical Parameters:
Prev
None
Next
More products
Desktop whole grain machine ZLJ-100
Working principle: The whole grain machine utilizes the high-speed relative motion between the rotor and the screen to quickly granulate the block-like materials under the pressure of the rotor, passing through the screen holes, and the finished granules are instantly discharged. It features low heat generation, high efficiency, and good quality. Variable frequency speed regulation allows for adjustable main shaft speed with a wide range. The bottom drive ensures smooth feeding.
Mobile whole grain machine ZLJ-208-Y
Working principle: This machine utilizes the high-speed relative motion between the rotor and the screen to quickly granulate the block-like materials under the pressure of the rotor, passing through the screen holes. The finished granules are discharged instantly, resulting in less heat generation, high efficiency, and good quality. It adopts frequency conversion speed regulation, the main shaft speed is adjustable, and the range is wide. The lower drive ensures smooth feeding. The parts of the machine that contact the materials and the external parts are made of high-quality stainless steel with a polished surface. It can be used with wet granulation machines and fluidized bed drying equipment.
Mobile Whole Grain Machine (Explosion-proof) ZLJ-100-EX
Working principle: The whole grain machine utilizes the high-speed relative motion between the rotor and the screen to quickly granulate the block-like materials under the pressure of the rotor, passing through the screen holes, and the finished granules are instantly discharged. It features low heat generation, high efficiency, and good quality. Variable frequency speed regulation allows for adjustable main shaft speed with a wide range. The bottom drive ensures smooth feeding.
Chongqing Liweikang's self-designed whole grain machine's right-angle transmission system and shaft sealing technology greatly reduces the risk of material contamination.
Get free product quotes
Our staff will contact you within 24 hours (working days). If you need other services, please call the service hotline: 023-65663700
* Note: Please be sure to fill in the information accurately and keep the communication unblocked. We will get in touch with you as soon as possible.
Contact Information
Telephone
/ TEL
Address
/ ADD
No. 2, No. 712 Xiangfu Avenue, Shuangfu Street, jiangjin district, Chongqing
Scan mobile websites
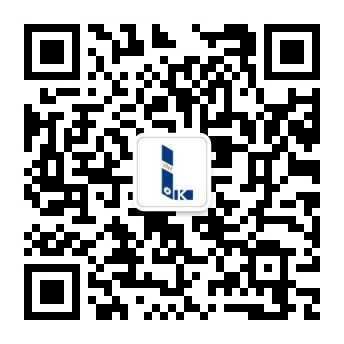