Multifunctional pellet making, granulating and coating machine
Equipment Description: The multifunctional granulator and coating machine adopts a modular design. Different functional modules can be added according to usage requirements, realizing the free switching of centrifugal granulation, extrusion rolling, and cutting spray granulation. Through the quick conversion of the rotating disc and the gear disc, the machine simultaneously has the functions of starting, granulating, coating, extruding, and rolling. It has two microsphere preparation methods: centrifugal granulation and tangential spray granulation. Finished microspheres can also be put into the material tank and sprayed with atomized coating liquid for coating. The microspheres have good sphericity, uniform size, and high drug utilization rate. They are suitable for sustained-release drug granulation, enteric-coated drug granulation, microsphere coating, and other processes. It is an ideal equipment for exploring microsphere preparation processes and formula development. The application of microspheres in the field of pharmaceutics is very extensive. As a drug carrier, it can be further pressed into tablets or put into empty capsules. This not only improves drug stability, but also effectively regulates the drug release rate; as a drug delivery system, microspheres have therapeutic advantages, such as less gastrointestinal irritation and reduced risk of drug bolus release, improving drug safety and good reproducibility of blood drug concentration; microspheres also have good fluidity, low friability, easy filling, and other processing advantages.
Key words: liquid particle handling system solid particle handling system pharmaceutical preparation intelligent equipment equipment intelligent control technology
Classification:
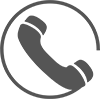
Hotline:
Multifunctional pellet making, granulating and coating machine
Device Description:
The multifunctional pellet making and granulating coating machine adopts a modular design, and different functional modules can be added according to usage needs to realize free switching between centrifugal pelletizing, extrusion rolling, and cutting spray pelletizing. Through the quick conversion of the rotating disc and toothed disc, this machine has multiple functions such as priming, granulating, coating, pressing, and rolling. It has two micro-pellet preparation methods: centrifugal pelletizing and tangential spray pelletizing. Finished micro-pellets can also be put into the material tank and sprayed with atomized coating liquid for coating. The micro-pellets have good sphericity, uniform size, and high drug utilization rate, suitable for sustained-release drug granulation, enteric drug granulation, micro-pellet coating, etc. It is an ideal equipment for exploring micro-pellet preparation processes and formula development.
Micro-pellets have been widely used in the field of pharmaceutics. As a drug carrier, it can be further pressed into tablets or filled into empty capsules, not only improving drug stability but also effectively regulating the drug release rate; as a drug delivery system, micro-pellets have therapeutic advantages such as less gastrointestinal irritation and reduced risk of drug burst release, improving drug safety and good blood concentration reproducibility; micro-pellets also have good fluidity, low friability, and easy filling.
In pharmaceutical production, compared with other pelletizing methods, extrusion rolling technology, as an advanced process method widely used in the international pharmaceutical industry, has the following characteristics:
- The process operation is carried out in a wet state, completely eliminating dust.
- Product yield exceeds 99%. The particle size distribution is narrow, and the qualified product rate reaches more than 90%.
- The micro-pellets have good roundness, good strength, and a density of 0.8g/cm3 or higher, which is conducive to producing film-coated tablets with uniform film.
- Micro-pellets have a large drug loading capacity, and the drug loading capacity has a wide variable range.
- It is easy to achieve mixing of incompatible active ingredients.
- Enzyme activity loss is small during enzyme preparation, as low as less than 10%.
- The single-line production capacity can reach up to 200kg/hour (production equipment), with high efficiency, low cost, and low labor intensity.
- Good process reproducibility, parameterized process parameters, easy to control, and easy to manage scientifically.
In controlled-release preparations and drug utilization, many factors in extrusion rolling pelletizing can change the powder properties and drug release behavior of micro-pellets—the measurement index of micro-pellet quality, mainly including: micro-pellet particle size, roundness, friability, density, fluidity, and drug dissolution and the microstructure of the micro-pellet surface, etc.—Through independent and detailed examination of various factors, the properties of micro-pellets can be improved to achieve the expected medication purpose.
Technical Features:
1. This machine innovatively has three micro-pellet preparation functions: centrifugal pelletizing, cutting spray pelletizing, and extrusion rolling pelletizing, and at the same time has centrifugal and side spray coating functions; different pelletizing modules meet the exploration of pelletizing processes for materials with different physical properties.
2. It innovatively adopts a brushless DC motor to drive rolling and extrusion, and a servo motor to drive the peristaltic pump head for liquid and powder feeding, increasing equipment reliability and service life.
3. The unique atomizer adjustment mechanism and diversion baffle can arbitrarily adjust the material movement trajectory at any position and angle, and the new atomizer makes the combination of material and binder atomized particles reach the optimal state, improving the pass rate.
4. The screw-type powder feeder has a bridge-breaking stirring device, and the powder feeding is continuous and stable; its lifting device can realize buried feeding, avoiding powder spillage.
5. The cutting tooth disc tooth shape is optimized, processed by a four-axis machining center, and dynamically balanced.
6. A cyclone separator system and a cylindrical filter system for gas-solid separation are configured to separate, recover, and filter the exhaust gas.
7. Configured with multiple process modules, using a touch screen + PLC control system, which can steplessly adjust the speed.
8. The structure is unique and novel, and the unique exterior arc design makes the appearance smooth and beautiful.
Technical Parameters:
Prev
None
Next
More products
Desktop whole grain machine ZLJ-100
Working principle: The whole grain machine utilizes the high-speed relative motion between the rotor and the screen to quickly granulate the block-like materials under the pressure of the rotor, passing through the screen holes, and the finished granules are instantly discharged. It features low heat generation, high efficiency, and good quality. Variable frequency speed regulation allows for adjustable main shaft speed with a wide range. The bottom drive ensures smooth feeding.
Mobile whole grain machine ZLJ-208-Y
Working principle: This machine utilizes the high-speed relative motion between the rotor and the screen to quickly granulate the block-like materials under the pressure of the rotor, passing through the screen holes. The finished granules are discharged instantly, resulting in less heat generation, high efficiency, and good quality. It adopts frequency conversion speed regulation, the main shaft speed is adjustable, and the range is wide. The lower drive ensures smooth feeding. The parts of the machine that contact the materials and the external parts are made of high-quality stainless steel with a polished surface. It can be used with wet granulation machines and fluidized bed drying equipment.
Mobile Whole Grain Machine (Explosion-proof) ZLJ-100-EX
Working principle: The whole grain machine utilizes the high-speed relative motion between the rotor and the screen to quickly granulate the block-like materials under the pressure of the rotor, passing through the screen holes, and the finished granules are instantly discharged. It features low heat generation, high efficiency, and good quality. Variable frequency speed regulation allows for adjustable main shaft speed with a wide range. The bottom drive ensures smooth feeding.
Chongqing Liweikang's self-designed whole grain machine's right-angle transmission system and shaft sealing technology greatly reduces the risk of material contamination.
Get free product quotes
Our staff will contact you within 24 hours (working days). If you need other services, please call the service hotline: 023-65663700
* Note: Please be sure to fill in the information accurately and keep the communication unblocked. We will get in touch with you as soon as possible.
Contact Information
Telephone
/ TEL
Address
/ ADD
No. 2, No. 712 Xiangfu Avenue, Shuangfu Street, jiangjin district, Chongqing
Scan mobile websites
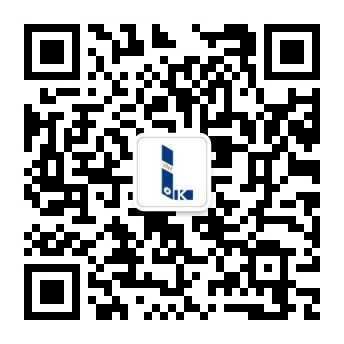